Sculptor Roberto Santo was standing in front of the trophy case at the legendary WinStar Farms in Kentucky, looking over the 100 or so statues given to the fastest horses to race in the Kentucky Derby, the Preakness Stakes, the Belmont Stakes, and dozens of other events around the United States.
The artist had just been asked by the New York Racing Association, Inc. CEO & President Chris Kay if he would think about creating a new Triple Crown Trophy that would be given to the winner of the Kentucky Derby, the Preakness Stakes, and the Belmont Stakes.
“I had some very serious thoughts about the Triple Crown Trophy,” Santo exclaims with a laugh. “I felt that what they had at the time didn’t feel like the ultimate trophy. The Triple Crown Trophy is the hardest trophy in the world to get. The possibility of it is almost nil.”
The Thoroughbred Racing Association commissioned the original Triple Crown Trophy in 1950. Each face of the three-sided vase featured information about the race, the horse, trainer, and jockey. While beautiful, it wasn’t stunning.
The new Triple Crown Trophy needed to stand taller and shine brighter than any other in the sport since the honor has only been given out 13 times since 1919. Justify is the most recent winner, earning the award in 2018.
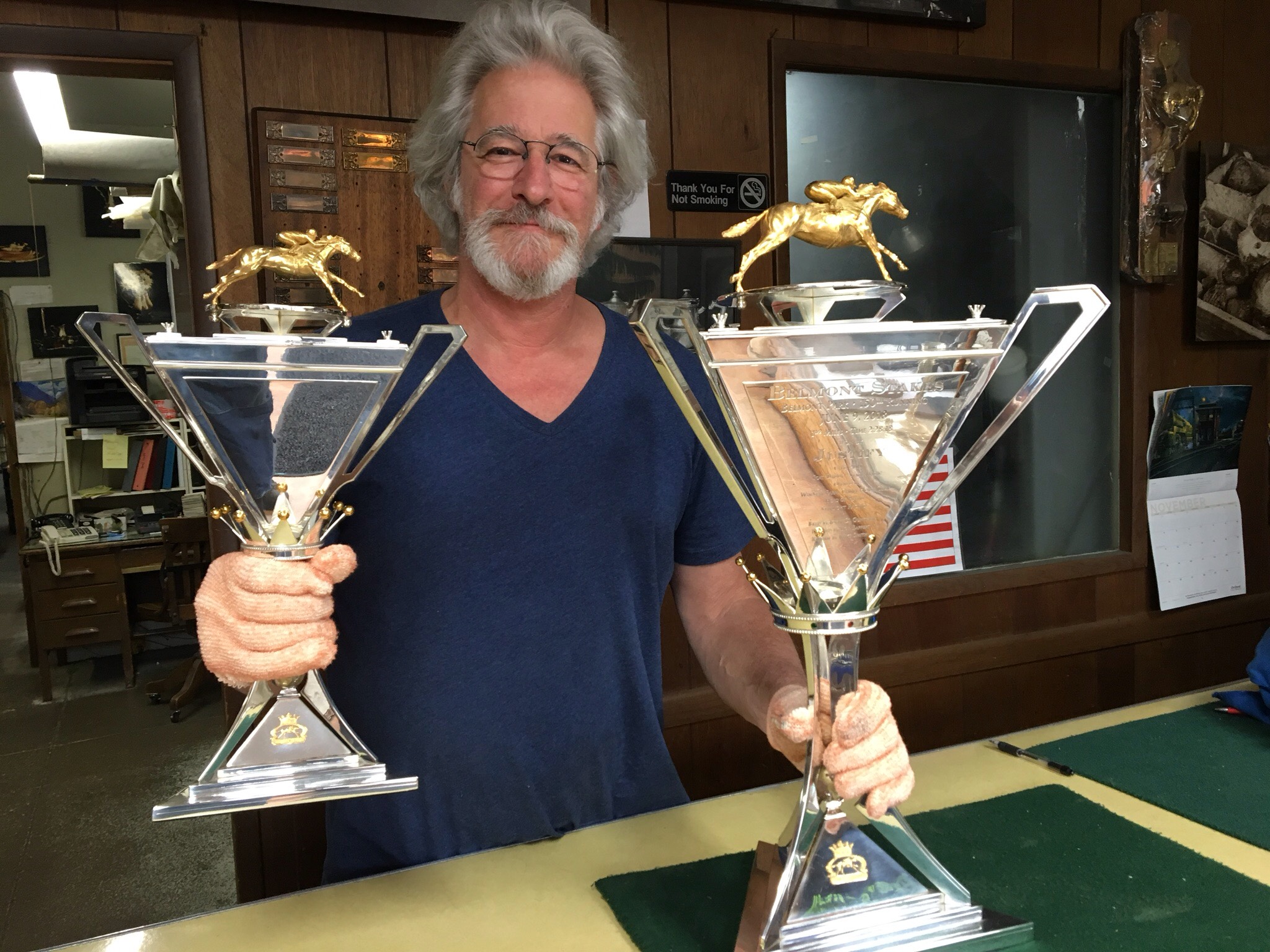
The Inspiration
Santo and Kay discussed broad ideas. Santo said he thought the trophy needed to mirror the honor. “It needed to be one of the biggest trophies, if not the biggest, in the history of trophies. It needed to show the magnitude of what it was.”
Kay concurred, and Santo launched into 10,000 hours of study. He visited horse farms, watched races, studied horse stride angles, looked at the trophies from other sports, and talked to people in the business.
Then he got to work. “I’m a conceptual dreamer,” Santo explains of his process. “All of a sudden, I saw this larger version of a triangular shape divided into three pieces with three uprights. The only singular piece on the entire trophy is the 14 karat gold horse on the top, which made sense to me because it’s about a singular horse. It’s not about three different horses.”
Before beginning sculpting the trophy out of modeling clay, Santo had some rough ideas about the trophy’s height, shape, and symbols.
“The Stanley Cup is 29-inches tall,” he reports. “Our trophy is 36.5-inches. So, right now this is the biggest trophy in the world, which is what we wanted.”
Santo felt it was essential to pay homage to the original trophy with a triangular loving cup. “The people in the horse business are enthusiasts, steeped in history and tradition. I thought we should take that essence and make it more 2016 (when the new trophy was created) than 1950.”
Symbolically, the trophy needed to represent the three tracks, and so he divided the entire concept into three equal parts.
And, of course, there’s the horse that sits atop the trophy. The NYRA had a contractual agreement that it could not emulate any of the winning horses. That made sense to Santo. “I thought that this horse had to be a combination of all the winning parts that make a horse spectacular in the racing world,” he says.
In addition to the physical attributes of a horse — color, size, etc. — one of the things that makes every animal unique is its stride angle. In general terms, the stride angle is the degree of the angle taken from the middle of the saddle to the front hooves and the back hooves — the greater the angle, the faster the horse.
Legendary horses share fairly large stride angles. For instance, American Pharaoh had a 104-degree stride angle. Secretariat, arguably one of the fastest thoroughbreds in the history of horse racing, had a 110-degree stride angle. The average horse, Santo discovered, is 97 degrees.
Adding that detail, he says now, was an essential ingredient to the trophy’s successful execution.
To get the detail he wanted to see in the finished horse, from stride angle to jockey’s crop, Santo sculped a 39.5” model that was then transformed to the 9.5” size that’s on the trophy.
Creating the Triple Crown Trophy
After the trophy met his vision, Santo created a smaller model that was cast in bronze, because that material holds detail better than others. That piece was refined, then silver-plated, then gold-plated for the shine, then dipped in silver, and then polished.
Santo worked with the legendary Ubaldo Vitali, a silversmith who has created and restored historical and noteworthy pieces of art during his 50-plus year career.
Read more about Mr. Vitali at this New York Times article.
Vitali has a long experience with racing trophies, including the one given to the winner of the Preakness Stakes. When Santo approached him about the new Triple Crown Trophy, Vitali said: “This will be my legacy,” Santo recalls, “which was a phenomenal compliment to give an artist.”
The Santo created, Vitali finished trophy is the one that stands next to jockey Mike Smith – at almost the same height! – in the Belmont winners circle when Justify won the most recent Triple Crown.
The original Triple Crown Trophy sits in a museum during the offseason and then travels from Churchill Downs to Pimlico Race Course and Belmont Park during those races.
The Owners’ Trophy
Given the historic nature of Justify’s Triple Crown win — only the second horse to win the honor with an undefeated record, following Seattle Slew in 1977 — the management at Churchill Downs, Pimlico Race Course, and Belmont Park decided to present a trophy to majority owner Kenny and Lisa Troutt.
Work on a smaller, 26” replica, started in 2018. Roberto worked in bronze again to capture the vital details from the original and then began working with a bronze fabricator, laser cutter, and a jeweler to design and manufacture the horses and crowns for the trophy.
Once all the pieces were built, Roberto needed to find a silversmith to bring it all together.
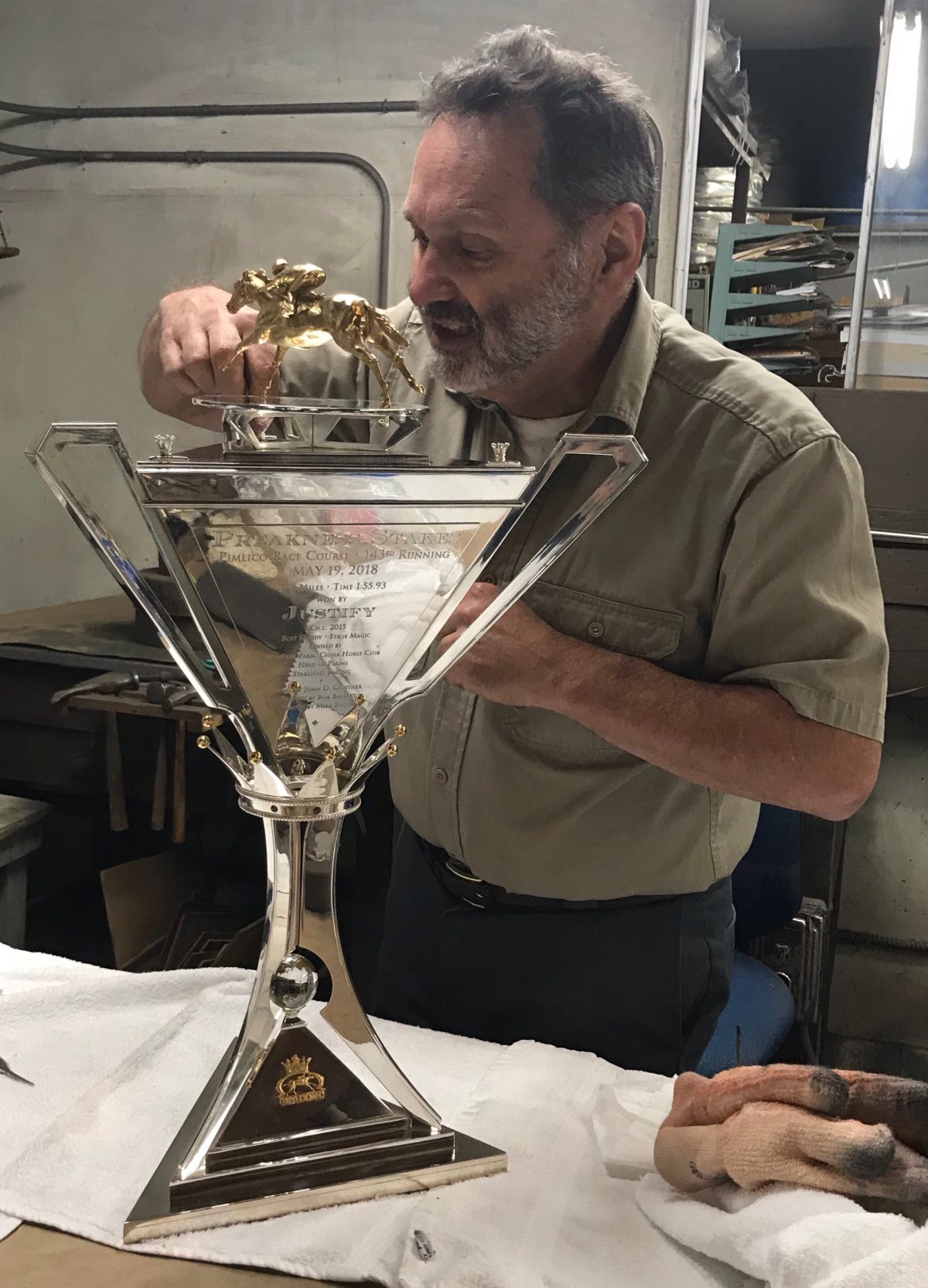
The Biro’s Involvement
Roberto talked to a lot of people before finding Biro & Sons, including artisans across the United States and Europe. He even interviewed quite a few silversmiths throughout the United States.
Then the phone rang at Biro’s in San Francisco. During the first call with Martin and Rick, Roberto felt it was a good fit. “There was genuine excitement from them,” Roberto recalls. “This wasn’t just another job. It was, ‘Wow, we could do something that will go down in history.’”
Santo took a look at some of the Biro’s past work and then traveled to San Francisco to make sure it was right. “I work intricately with people, even though they do the craft that they do,” he says. “I’m involved because the end product has my name on it and the end product has to be exactly what I anticipated.
“And I like dealing with people that know their craft, and that understand the material,” Santo continues. “Martin and Rick and the whole group there are that. I have a real affinity to both of them now and the whole team there.”
He also connected with Martin and Rick over their shared experience working in the family business. “I grew up in a similar environment,” he says. “My Dad [illustrator Bob Peak] was a very famous artist, so I grew up with that, and they grew up with the silversmith concept their whole lives.”
Rick concurs. “You never know how the chemistry is going to work when you’re working with a new client, but Roberto’s commitment and passion to the project made the whole process great.”
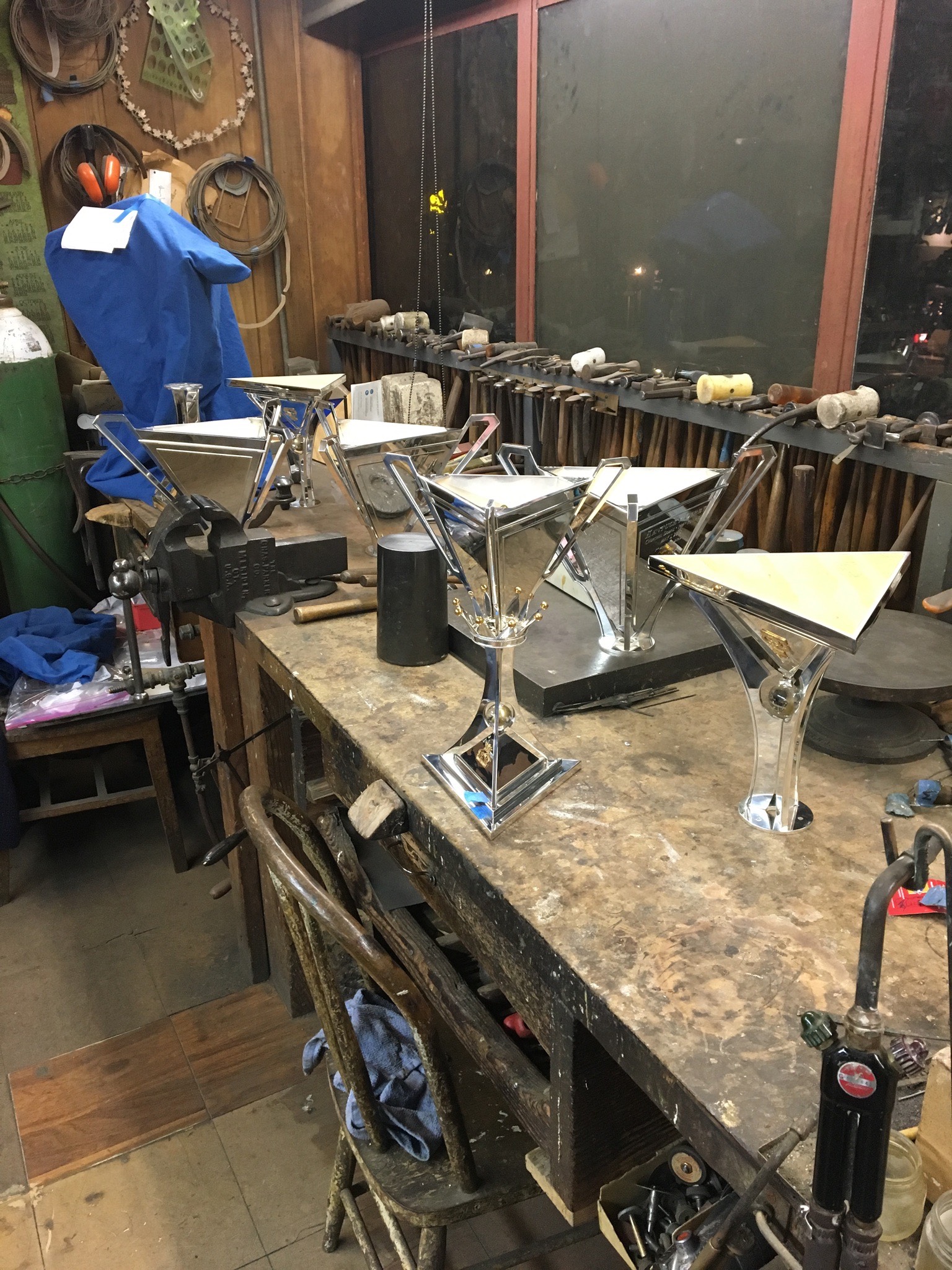
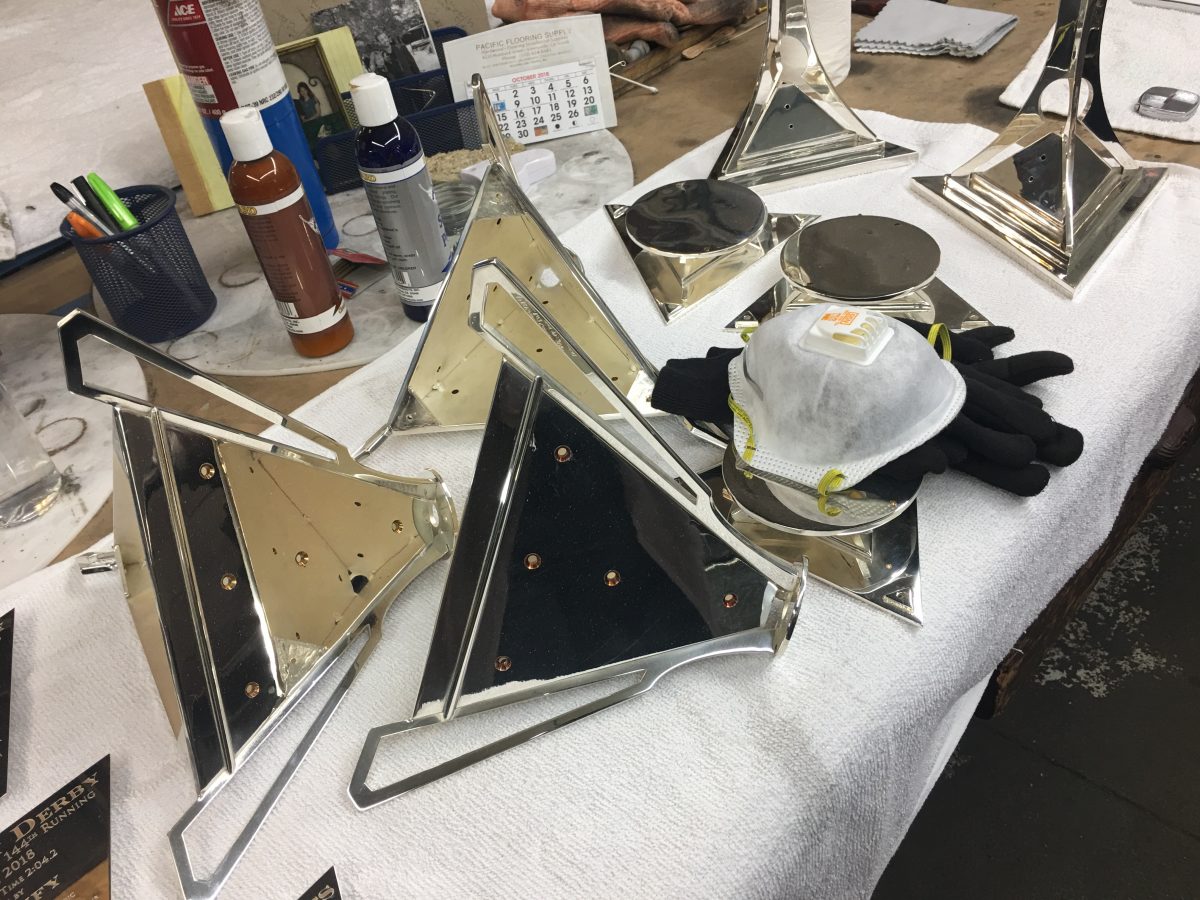
Putting the Trophy Together
Roberto, Martin, and Richard worked for just over a year to get perfect results.
Roberto delivered all the pieces — the bronze loving cups, the glass balls, the horses and crowns from the jeweler — and then the Biro team assembled it. When it was all said and done, the Biros delivered eight 26″ trophies for the ownership group and four 18″ trophies for the rest of the team.
Martin managed the building and plating. Rick took on the fine details.
Santo was impressed with both.
One example: the handmade crop on the horse. “There was no way to cast a crop that’s an inch long and the thickness of a needle,” he says. “That was crafted by them to copy what I had on my original model. Then there were the reins, which they had to do completely. They did a great job.”
Another example is the silver soldering that brought all the pieces together with strength and beauty. “It adds this beautiful effect to the trophy,” Santo says, “so that if you look closely, you can see the care and craftsmanship that went into it.”
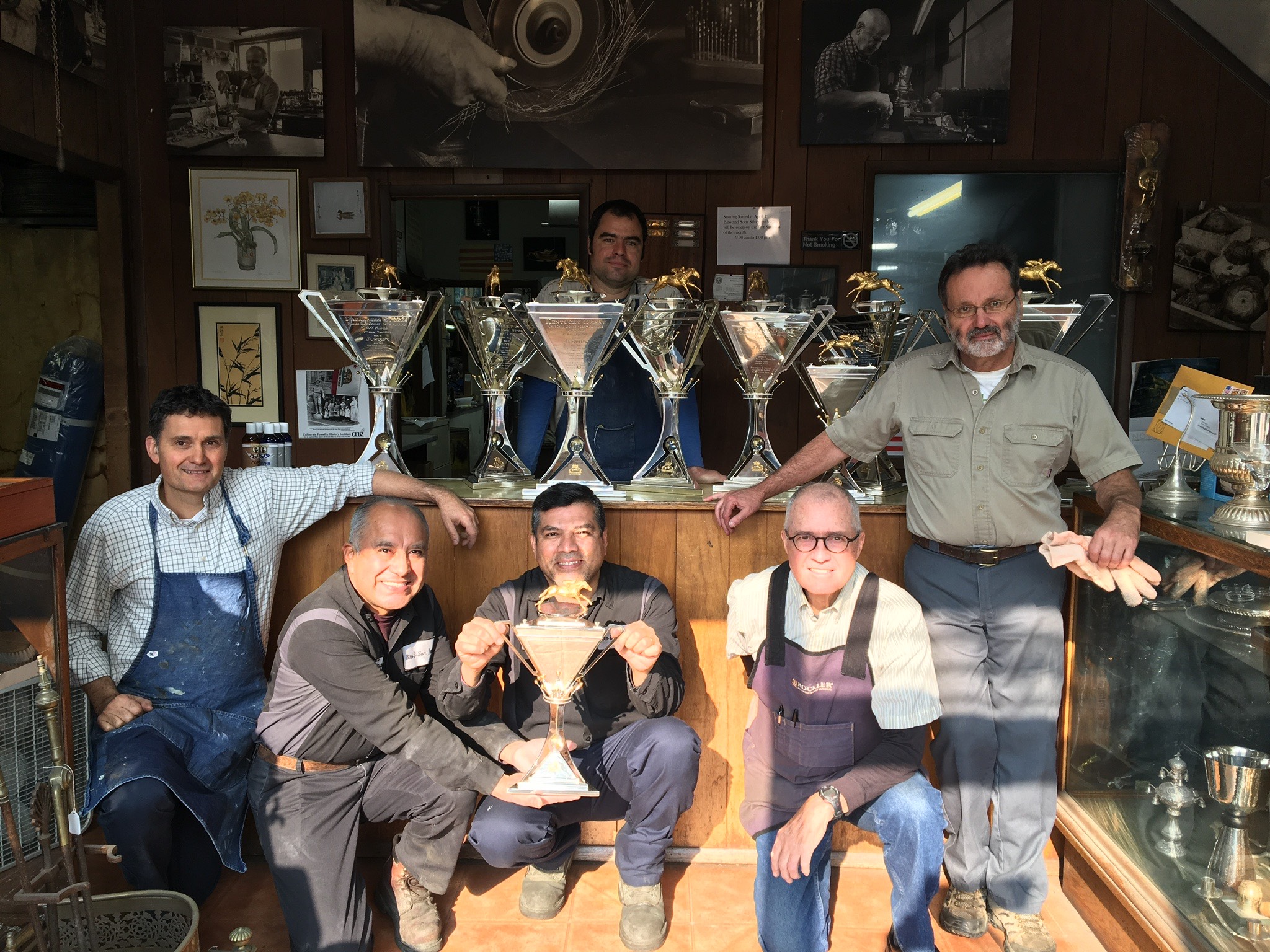
The Results
The camaraderie and skill were crucial for Santo, especially for how long it took to get to the finished project.
“The Biros understood how much I wanted this trophy to be unbelievable,” Santo says. “That that was important to me. And they realized that they wanted to do something unbelievable as well. So, it worked hand-in-hand.”
Santo knows that’s true because during another visit to WinStar the new Triple Crown Trophy was in the case. “We were standing there, and one of the people there said to me, ‘Wow, this trophy separates itself from the rest.’ That’s what I was going for, to do something that separated from the norm.”
It was an honor for the Biro team as well. “We were very fortunate to work on such a significant trophy in the horse racing community,” says Rick Biro. “We realized that fabricating it would be challenging, but it was a great experience.”